E2R PGC
Are you overwhelmed by the number of production processes?
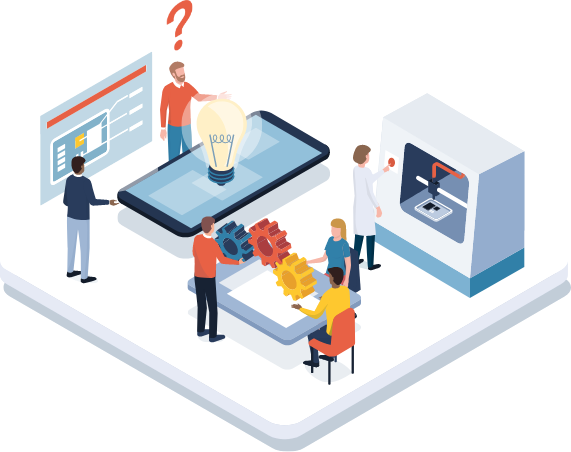
What about having them all under control?
Choose the best module for your company.
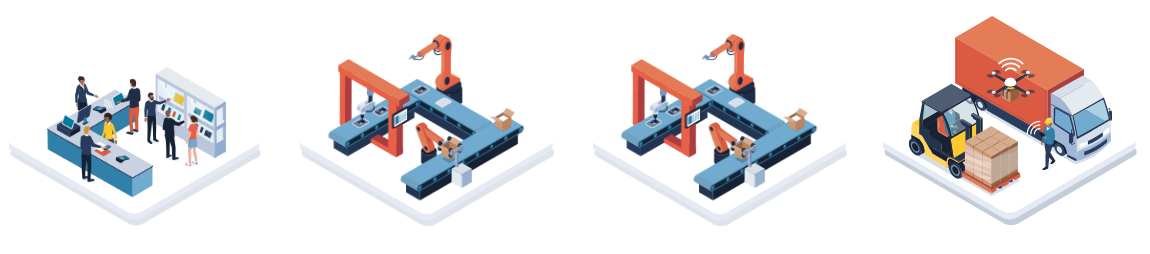
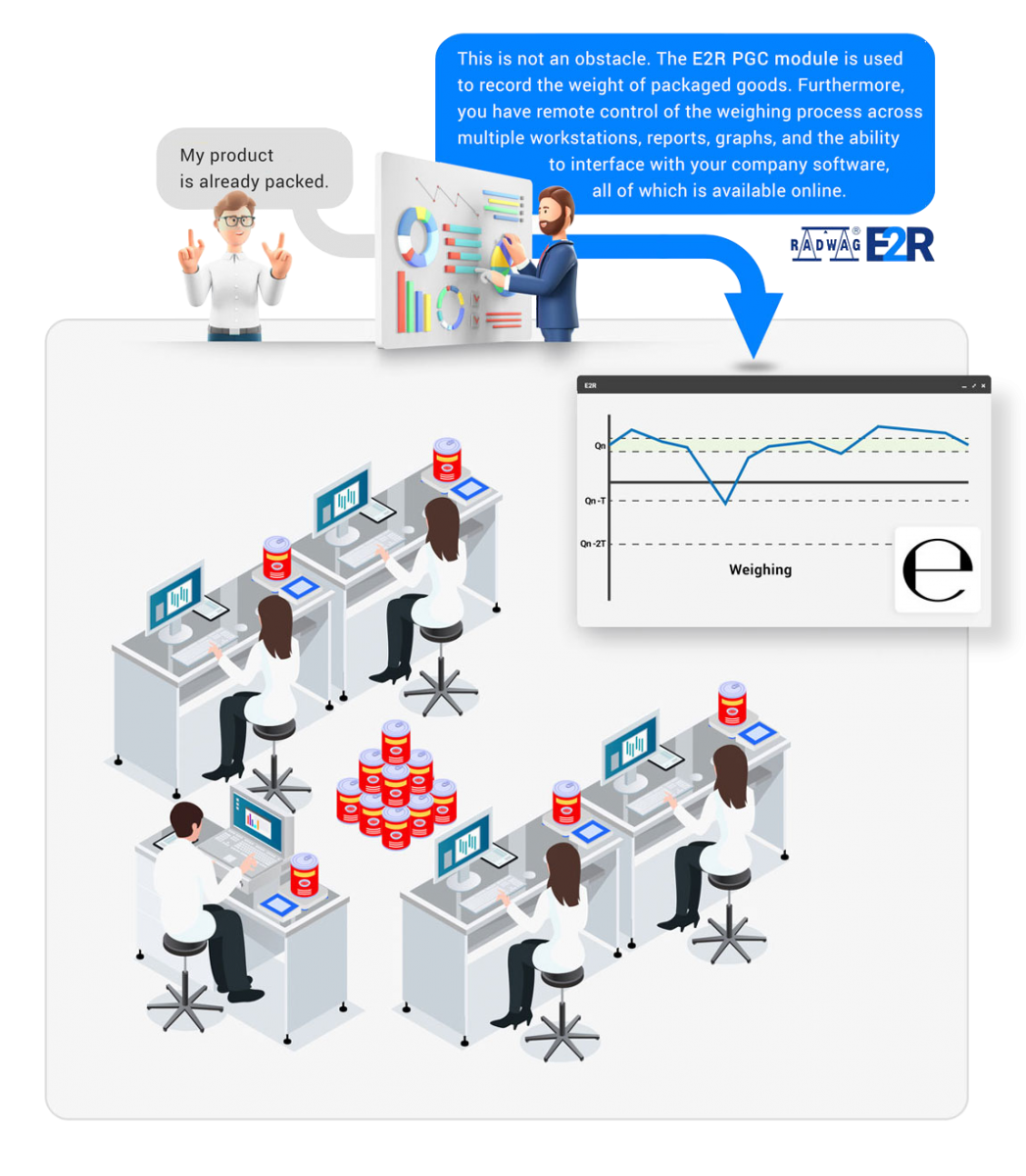
Need more information?
- safely and continuously record measurements and controls at the weighing workstations;
- buffer the weighings and controls on the scales and transmit them to the computer;
- carry out product controls in grams and millilitres;
- carry out destructive and non-destructive controls;
- automate the control process;
- control operator errors;
- support dual-platform scales;
- carry out two controls at one weighing workstation;
- synchronise time of the weighing workstations;
- transfer the “Products”, “Operators” and “Schedules” databases from the computer to the scales;
- schedule a cyclic product control on the selected scales;
- set a reminder to take a measurement in an ongoing control with the possibility of using a signalling option;
- check correctness and determine tare thanks to the average tare module;
- determine the average tare before each control or at the set interval;
- record weighings and controls taken from the scales into the computer;
- monitor the status of scales and controls in the system;
- disable the measurement recording for tare outside the tolerance range;
- disable the recording of the net mass measurement outside the tolerance range;
- exchange data with external systems;
-
use friendly and flexible reporting mechanisms, such as:
- generating information on measurements and archived controls from a particular time interval,- data browsing using filtering option,- a summary of selected weighing-related information,- reporting of individual weighings,- determining headers of individual weighing reports,- generating weighing statistics reports,- changing the batch quantity in the control to meet the statutory ranges criteria,- changing the batch number in the control,- adding individual comments to the control report.- export control and weighing reports to files: PDF, HTML, MHT, RTF, XLS, XLSX, CSV, TXT and more;
- customize the permission levels for different users of the system;
-
customize the graphical interface, reports and graphs;
- work with external software for stockpiling, billing, accounting, and ERP systems;
- work with RADWAG weighing systems;
- select the language of each of the system components;
- work almost anywhere over Ethernet and Wi-Fi®.
Wi-Fi® is a registered trademark of Wi-Fi Alliance®.